The problem: Extensive time required for scaffolding during a maintenance outage
Many boiler operators, particularly those in the energy from waste sector, need to regularly shut down their plant for maintenance. As soon as the installation has been transferred from “Operations” to “Maintenance”, the clock starts ticking for the latter. Every hour that the installation is out of service is a significant expense. Moreover, it takes quite some time, especially with larger boilers, for the installation to cool down in such a way that it can be worked on safely. The first concern of the outage manager is usually aimed at building up the necessary scaffolding as quickly as possible and getting it approved. During planned maintenance outages (but also in the event of unforeseen events), the scaffolding often first has to be designed, reviewed and then safely installed. At the end of the outage, the scaffolding has to be dismounted and removed. The time required for this work adds to the total maintenance cost. These scaffolding costs alone can in some cases amount to -very- substantial amounts and are often an annual or bi-annual recurring burden for the plant operator.
The solution:
An efficient solution was devised based on the lessons learned during the supervision of many maintenance outages at the plants of Hilux5 customers. Our engineers developed a smart scaffolding system that enables fast and consistently safe installation of large scaffolding structures. With energy from waste boilers, the 'smart scaffolding' makes it possible to work on the boiler grate and on the boiler radiant cell at the same time. Because the system is standardized, after the construction has been approved once, no additional inspections are required. The 'smart scaffolding' can be used safely again and again at each subsequent outage and usually pays for itself after only one or two maintenance outages! No wonder that this system is already used by many of our customers.
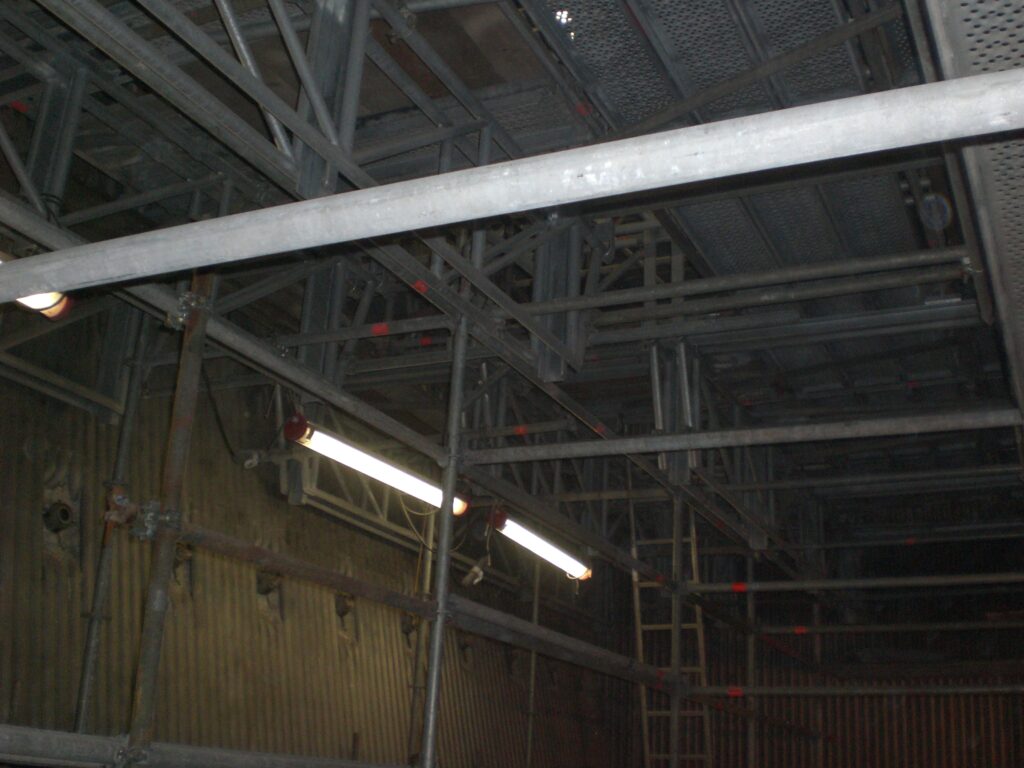